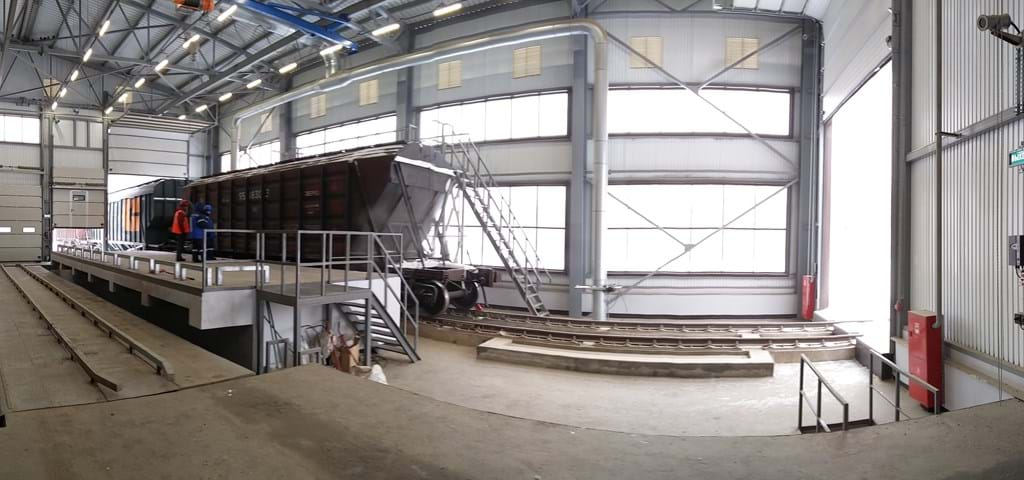
Yet another exciting project
It´s hard not to be stunned by this large feed mill project - also with train station
– when seeing the trains arriving and the wagon just unloads the grain into the intake.
Corall LLC has made an impressive green field farm-to-table project. The green-field project consists of a 22 ton/hour feed factory for their pork producing farm with 16,000 sows, capacity of 450.000 head/year and a modern meat processing plant.
The feed factory, the pig farm and the modern slaughterhouse are located in the Tver region close to each other.
“We want to produce high-quality food which is traceable and in a closed circle which we totally control, so the bio-security is a top priority. This is a huge project, with modern and top quality facilities from the pig farm to the feed mill and to the slaughterhouse“, tells Mr S.V. Chmykhalov, CEO of Corall.
“A high feed quality is one of our highest priorities, and the feed mill from SKIOLD should improve our efficiency and feed the pigs with better feed for higher efficiency and animal health. The feed mill is now running, and we are very satisfied with the results” ends Mr Chmykhalov.
The feed factory is a full line project
After the grain goes into the intake, grains and other macro components are stored in raw materials silos before dosing. A transport system conveys the raw materials to the silos. The raw materials are ground in a hammer mill.
The mill is equipped with a separator with a permanent magnet, which removes magnetic metallic impurities as well as other heavy impurities before the raw material is sucked into the milling chamber. The milled product falls into a mill bin. A discharge auger empties the bin continuously.
Small component proportioning is used for the addition of small quantities of e.g. vitamins, minerals etc. The components are stored in bins from where they are dosed and transported to a central weigher suitable for precise weighing of small quantities. The automatic micro components dosing plant reduces the number of premixes required, saves labour and improves the weighing accuracy.
An accurate mixing is of vital importance for the feed quality. The dry products are gently mixed in the horizontal paddle type mixer. For full utilization of the mixing capacity, the mixer is provided with both pre- and discharge bins which act as buffers.
The pelleting section comprises a row of single machines that transform meal feed into pellets. Meal feed is dosed into the Conditioner where after steam is added for heat treatment and gelatinization of the meal feed which makes it easier to pelletize and leads to a higher pellet durability. After the meal feed has been pressed through the matrix, which is optional as to the size of diameter and thickness, the hot pellets fall directly into the cooler cooling the pellets from approx. 80° to just above room temperature. When producing starter feed, it is necessary to crumble the pellets into granulate by means of a crumbler or to use a die with relatively small holes. Finally, the pellets are sifted and cleaned ensuring dust-free pellets. The ready feed silos act as buffers for bulk feed before use or road transport to the final destination.
A central control panel with the advanced Flexmix PRO computer allows the feed mill operators to control, operate and supervise the entire operation of the feed mill.
The Flexmix PRO computer is used for programming of recipes, production orders etc. and also saves information about productions, current stock level etc. in a database which also creates various relevant production reports.
Contact us for more information