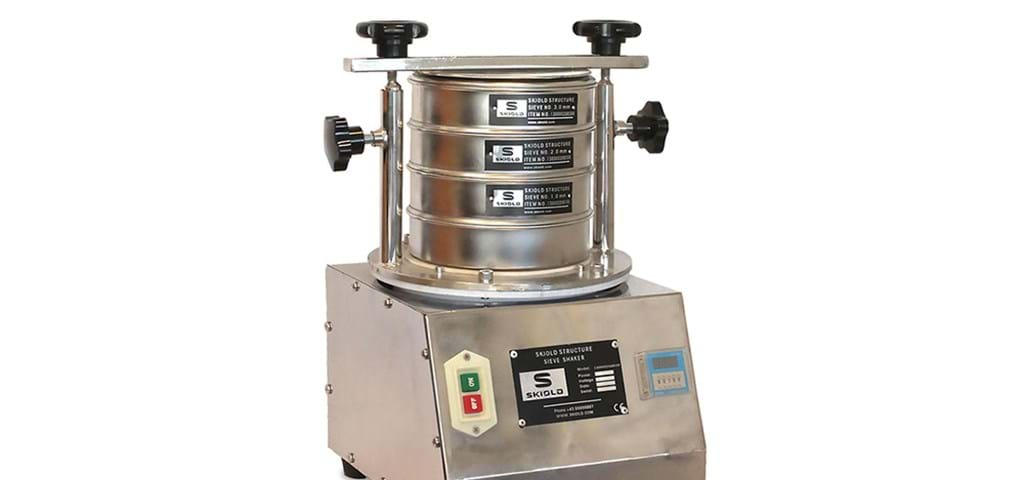
Accurate grinding pays off
Better feed utilization and healthier stomachs
In recent years, there has been an increasing focus among farmers on producing feed with just the right degree of grinding. The reason for this development is a clear economic incentive: the more precisely the feed is adapted to the animals' needs, the lower the feed consumption per kg gain - and this can be felt directly on the bottom line.
In both weaners and finishers, it is well documented that finer grinding improves feed utilization. However, the challenge with very fine grinding is an increased risk of gastric ulcers, which can lead to large financial losses if not detected and dealt with in time.
Therefore, there is an increasing focus - among consultants and veterinarians alike - on not only the degree of grinding, but also the feed structure and particle size distribution. For many years, there have been recommendations for how large a proportion of the feed should be below 1 mm, but new knowledge indicates that the distribution of fine particles below 1 mm also plays an important role.
This increases the requirements for feed control - and places correspondingly high demands on the equipment used to analyze the grinding.
Advanced analytics provides new insights
For a number of years, SKIOLD has offered a professional sifter that quickly and accurately analyzes the sieve profile of ground barley or wheat. Despite this, many still choose to use manual solutions such as the classic barley sieve or SKIOLD's own “cookie jar sieve” with a 1 mm sieve.
These manual methods require both patience and precision - and provide no insight into how the very fine particles below 1 mm are distributed. With SKIOLD's professional screening equipment, which is equipped with 1, 2 and 3 mm sieves as standard and can easily be expanded with 0.25 and 0.5 mm sieves, you get a much more nuanced picture of the particle profile - down to the smallest fractions.
Several analyses have shown how much savings can be achieved by reducing feed consumption by just 0.1 FU per kg gain. That's why it's crucial to use the right analytical methods in the quest for optimization.
Choice of mill is of great importance
Feed is typically grinded using one of two principles: either a hammer mill or a disk mill. The hammer mill has been standard for over 60 years and works on a simple principle with rotating flails and screens. SKIOLD's disc mill, on the other hand, is based on a unique technique where two discs work against each other and allow for stepless adjustment of the grinding degree - with significantly lower energy consumption.
Although both mill types are suitable, they do not produce the same particle profile. It's well known that older hammer mills with built-in blower blades in particular create large amounts of very fine particles - the so-called “baking flour” - which is unhealthy for stomach health. Many of these older mills are still in operation, although they are gradually being phased out.
Modern mills offer more control and lower costs
Replacing older mills with a modern hammer mill or disc mill offers a number of benefits: better control of the grinding degree, lower power consumption, less dust generation and a lower noise level.
SKIOLD supplies both hammer and disc mills in different sizes and configurations - and we are always ready with advice to ensure the optimal solution for your farm.
Want to know more about SKIOLD's mills?