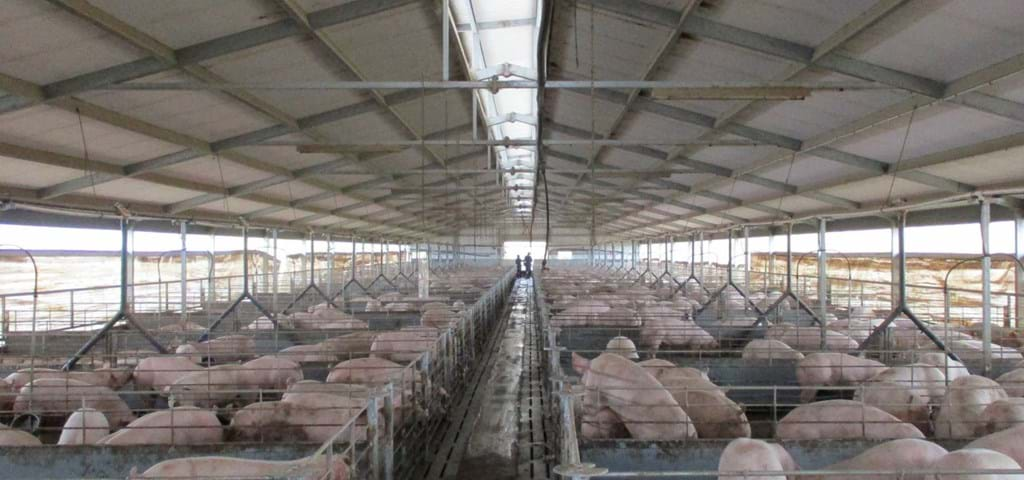
Clarrich Farm, Australia
3 tonne SKIOLD liquid feeding system for the growing progeny of 1000 sow farm
Clarrich Farms runs a 2 site (Breeder-Grower), 1000 sow operation in Northern NSW region of Australia. In May 2016 the Clarrich Farms Grower Unit commissioned a twin batching, 3-tonne SKIOLD liquid feed system for the growing progeny of our 1000 sow farm.
From Denmark to Australia: A seamless partnership for smarter pig feeding.
The group decided on this high tech feeding approach, in the main the reach a better feed conversion level for our farm. We could have just implemented a normal technology, dry feeding system, but the benefits of up to 5% feed gain ration in a world with rising feed costs, was the correct financial decision for our group. said, MD Geoff Handley.
Our nutrition advice was that the 4 times per day feeding will give better animal health – digestibility outcomes; the precise feeding level per pig will give better carcass quality outcomes; the ability to phase feed within shed groups rather than whole sheds/silos as a single group; the long trough feeding will allow better market weight selection when marking up sales at feeding time, as well as better noticing “fall-back” animals; and finally we will be able to tap into by-product supplies if they become available.
Geoff Handley: “The system is delivering all the benefits predicted—and more.”
It is our experience after using the system for 16 months now, that the SKIOLD system is delivering all the benefits that were predicted said Mr.Handley. We have not yet sourced by-products, but that project is now top of our list to be able to reduce feed input costs.
Being at a distance, the recommendation to run a twin batching system was a good one. We did get some electrical boards wet in sea transit (not SKIOLD’s issue) and did need to run the system for a week on a single mixer. We switched to larger batch sizes with 3times per day feeding rather than 4 and extended the hours of operation while waiting for parts to be flown in. The system worked very well in that crisis situation, and we now carry a few more spare parts for future proofing of that issue.
The SKIOLD team supported us from the first step when we visited their showroom in Denmark, right through to the 10-day final set-up and commissioning. As with all systems, there were teething problems, but the 24/7 support team were always there to get online and sort our issues. Being so far away, the support system was our most worrying part, and SKIOLD has shown that their system and follow-up post issue has been without fault. We had our 12-month service in May when the last non-serious issue was resolved on site by their technician, and the last 2 months have been free of any issues.
We have been very pleased with the results from the system, and the ongoing support of SKIOLD and have no hesitation in recommending them to potential users.” ends Mr Geoff Handley