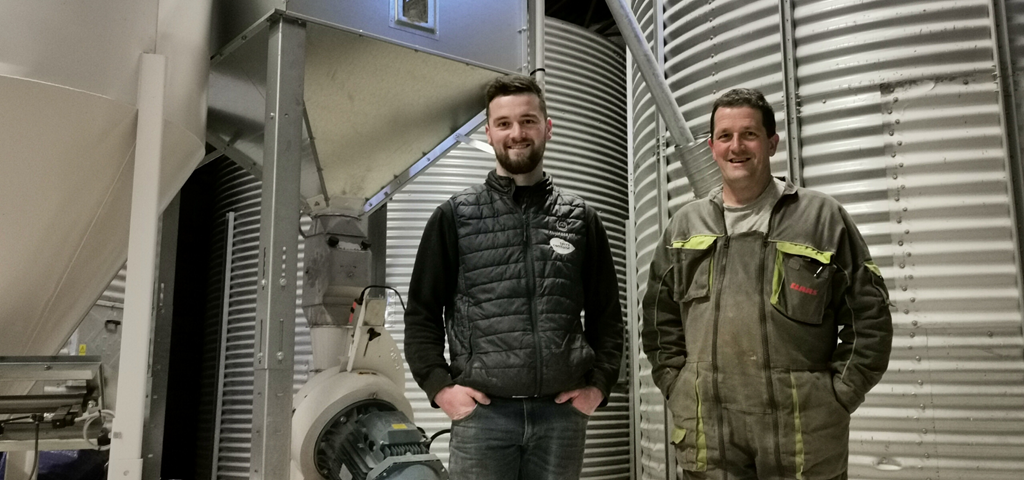
The feed mill quickly paid for itself
Economically speaking, it is profitable. We can do a lot with less
In the Haute Saône, the GAEC de l'Aigle produces an average of 365 tons of Emmental Grand Cru per year. "Hmmm, a real piece of Emmental!"
Since the end of 2019, the 85 dairy cows have been fed with feed made on the farm. Jean-Charles and Julien, father and son, decided to invest in a feed factory to reduce costs: "We managed to control almost all our expenses except those for feed. It was the most expensive item with nearly € 80,000 not counting the barley and corn that we produce ourselves. To reduce it, we decided to manufacture on the farm."
Thanks to their feed factory, they manufacture 400 tons per year (including 150 tons of farmhouse mix).
How long did it take to make your on-farm feed mill project a reality?
Decision to invest in on-farm feed production
"We moved very quickly! I joined the GAEC on 1st of August. We signed the in September.
I was already working on the farm and had visited a farm where they did a lot on their own. They had a lot of semi-finished products. And I thought, "We have to do this. That was the trigger. He earned €40 per tonne on the oilcake alone."
It all started when they discovered an offer on Agriaffaires. "Even before contacting a distributor, we went to Bordeaux, to a breeder who wanted to sell everything on his farm to start cognac production. One of the buildings was full of storage silos. We dismantled 6 silos and brought everything back here. It's easy to disassemble but it takes time. This is how we got to know about ACEMO: Thanks to the silos. Then we contacted the distributor Alfadou, and we asked Anthony what he was selling. He said ACEMO. You have a sales representative in our sector and then we were well advised and given addresses. But we never visited other farms. We were convinced of what we were doing."
Installation & Assembly of the factory
"Even if the factory arrives pre-assembled, it's a lot of work to assemble:
- 1 day per silo
- 3 days for sockets and pipes above
- 2 days for augers
- 1 week for wiring
- 1 month and a half for concrete
After that it was small mechanics."
Why did you choose the SKIOLD brand?
"What made the difference:
- The weighing system and the automation. We didn't want to spend our time pressing buttons, being on the sideline to monitor. We wanted something that would do it automatically. The automation is very easy to handle, scalable and you can do a lot of things with it. There is nothing bad to say.
- The Disc Mill: No noise, no dust and good flow rate. I can grind 1 ton in less than 45 minutes. The disc distance is 0.7 or 0.8. The animals like it."
What did the feed factory bring us?
"We only spend one hour pr month to operate the feed mill and we have 7 recipes:
- 3 for VLs
- 2 for heifers
- 1 for bulls
- 1 for calves
And that's just the beginning! The advantage is that here you have a multitude of raw materials and possibilities: Barley, triticale, maize, and we still have soybean, rapeseed. and then we will bring in beet pulp and corn.
And economically speaking, it is profitable. We can do a lot with less. And then, we are autonomous and we know where we are going. We know what we give. We are less careful about giving 1 kg of feed extra. This helps smooth out costs and improves our cash flow. Especially during the winter months. "
Feed for young bovine animals |
Protein concentrate 22
|
![]() |
Feed for dairy cows |
Farmer blend
|
![]() |
Feed for dairy cows |
Protein meal 40
|
![]() |
For bulls |
Protein meal 36
|
![]() |
The results?
"The feed mill was launched on December 20th 2019. I produce a farm mix for 150€ (incorporating mineral and antacid). Of course, we have to take our manpower, handling, power and investment into account too, but overnight, we had results for the dairy:
- 2.5 fat point
- 1.5 point of TP at 6€
- +2.5 L of milk per cow
- 50€ for 1000 L of extra milk
The factory pays for itself quickly. Equivalently, we earned €60 per tonne knowing that we bought 250 tons of feed per year."
Any advice for breeders who want to invest in on-farm feed production?
"Incorporate minerals from the beginning, because the automation is able to handle it. Today, we have to be nearby to incorporate the salt. And we would put in smaller silos that we would fill more regularly. Otherwise nothing to complain about!"
Installation carried out by SKIOLD France' distributor Alfadou.
Do you want to make your own cattle feed? Contact us to find out more about our customisable feed milling solutions:
CONTACT US FOR FURTHER INFORMATION
Farm information:
- GAEC de l'Aigle, feed mill for cattle feed
- 3 partners
- 85 dairy cows
- 260 ha of UAA
- 7800 litres of milk on average per cow
- Dairy reference: 800,000
- SKIOLD MV600 feed factory: Disc Mill, 600 kg vertical mixer (V600), control by Fabristar control box – commissioned in 2019